Introduction to Chemical Reactor Analysis
7.290 kr.
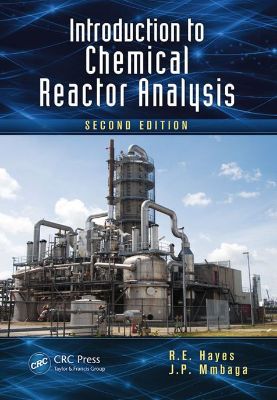
Námskeið
- EVF602M Hönnun efnahvarfa
Annað
- Höfundur: R.E. Hayes
- Útgáfa:2
- Útgáfudagur: 2012-10-05
- Hægt að prenta út 2 bls.
- Hægt að afrita 2 bls.
- Format:ePub
- ISBN 13: 9781439867013
- Print ISBN: 9781138434523
- ISBN 10: 1439867011
Efnisyfirlit
- Front Matter
- Dedication
- About the Book
- Preface
- Acknowledgments
- Recommended Reading
- Reaction Engineering, General, and Basic Books
- Reaction Engineering and Related Issues, More Advanced Books
- Reaction Engineering, Catalysis, and Catalytic Reactors
- Catalyst Preparation
- Thermodynamics
- Transport Phenomena, Including Mass, Heat, and Momentum Transfer
- Physical and Chemical Properties
- Mathematical Methods
- Nomenclature
- Greek Letters
- Abbreviations
- Authors
- 1 Introduction
- FIGURE 1.1 Illustration of some possible products that can be made from natural gas using chemical reactors. The symbol R in a box denotes a reactor and S denotes a separator. Each reactor is operated differently. Note that not all reactants and/or products present are shown in each case.
- 1.1 Process Development
- 1.2 Basic Building Blocks of Chemical Reaction Engineering
- FIGURE 1.2 Illustration of the relationship of kinetics, reactor analysis, and reactor design to the main areas of the chemical engineering curriculum.
- 1.3 Outline of the Book
- 1.4 Introduction to Chemical Reactions
- 1.4.1 Rate of Reaction
- 1.5 Classification and Types of Reactors
- 1.5.1 Batch and Semibatch Operation
- 1.5.1.1 Batch Reactor
- FIGURE 1.3 A typical batch reactor that may consist of a stirred tank containing the reactants. There are no inlet or outlet streams present during operation.
- 1.5.1.2 Semibatch Reactor
- 1.5.1.1 Batch Reactor
- 1.5.2 Continuous Flow Reactors
- FIGURE 1.4 A semibatch reactor that may be a well-stirred tank reactor to which material is added during the operation. For a liquid-phase reaction with no effluent stream, the reacting volume will increase with time.
- 1.5.2.1 Perfectly Mixed Flow Reactor
- 1.5.2.2 Plug Flow Reactor
- FIGURE 1.5 Illustration of a typical well-mixed continuous flow reactor. When the fluid in the reactor is perfectly mixed, the temperature and concentration are the same at every point in the reactor.
- FIGURE 1.6 Velocity pattern in a plug flow reactor. The velocity is uniform across the diameter. Concentration and temperature are also assumed to be constant across the diameter.
- 1.5.1 Batch and Semibatch Operation
- 1.5.3 Classification by Number of Phases
- 1.5.4 Catalytic Reactors
- 1.6 Reactor Performance Measures
- 1.6.1 Conversion
- Example 1.1
- SOLUTION
- Example 1.1
- 1.6.1 Conversion
- 1.6.2 Space Velocity
- 1.6.3 Liquid Hourly Space Velocity
- 1.6.4 Gas Hourly Space Velocity
- 1.6.4.1 Space Time
- 1.6.4.2 Residence Time
- 1.8.1 Material Balances
- 1.8.2 Energy Balance
- 1.8.3 Momentum Balances
- 1.8.4 Coupling of Material, Energy, and Momentum Balances
- 2.1 Basic Definitions
- 2.1.1 Open and Closed Systems
- 2.1.2 Thermodynamic Standard State
- 2.1.3 Equations of State
- 2.1.3.1 Ideal Gas Law
- 2.1.3.2 Nonideal Gas Behavior
- 2.1.4 Multicomponent Mixtures
- Example 2.1
- SOLUTION
- Example 2.2
- SOLUTION
- Example 2.1
- 2.2.1 Enthalpy
- 2.2.2 Energy Change Resulting from Temperature Change: Heat Capacity
- Example 2.3
- SOLUTION
- Example 2.3
- Example 2.4
- SOLUTION
- 2.2.4.1 Computing the Enthalpy of Reaction at Other Temperatures
- FIGURE 2.1 Alternate calculation pathway used to compute the enthalpy change of reaction at different temperatures and pressures.
- Example 2.5
- SOLUTION
- 2.3.1 Derivation of Equilibrium Constant
- 2.3.2 Computing Standard Free Energy Change
- 2.3.3 Temperature Dependence of Equilibrium Constant
- 2.3.4 Computing Equilibrium Composition
- 2.3.4.1 Liquid-Phase Reactions
- 2.3.4.2 Gas-Phase Reactions
- Example 2.6
- SOLUTION
- Example 2.6
- 2.3.4.3 Solid-Phase Reactions
- Example 2.7
- SOLUTION
- Example 2.7
- 3.1 General Mole Balance Equation
- 3.2 Perfectly Mixed Batch Reactor
- 3.2.1 Constant-Volume Batch Reactor
- 3.2.2 Variable-Volume Batch Reactor
- Example 3.1
- SOLUTION
- a. Constant-Volume Batch Reactor (CVBR)
- b. Constant-Pressure Batch Reactor (CPBR)
- c. Imposed Volume Change with Time
- Summary of the Three Cases
- SOLUTION
- Example 3.1
- 3.3.1 Plug Flow Assumptions
- 3.3.2 Plug Flow Mole Balance
- FIGURE 3.1 Volume element of a plug flow reactor used to develop the mole balance equation.
- 3.3.3 Space Time in Plug Flow Reactor
- 3.3.4 Mean Residence Time in Plug Flow Reactor
- Example 3.2
- SOLUTION
- Mean Residence Time
- Example 3.2
- FIGURE 3.2 A CSTR typically consists of a fluid-filled tank which is stirred by an impeller. Baffles are usually used to ensure good mixing.
- 3.4.1 Space Time and Mean Residence Time in CSTR
- Example 3.3
- SOLUTION
- Mean Residence Time
- Example 3.3
- Case Study 3.1: Hydrogenation of Sulfur and Nitrogen Compounds in Oil
- BATCH REACTOR OPERATION
- PLUG FLOW REACTOR
- CONTINUOUS STIRRED TANK REACTOR
- FIGURE 3.3 Representation of the rate behavior as a function of conversion for “normal” kinetics. The reaction rate decreases as conversion increases.
- FIGURE 3.4 Reaction rate behavior verses conversion for “normal” kinetics. The hatched area corresponds to the volume of a PFR required to give the indicated conversion.
- FIGURE 3.5 Reaction rate behavior verses conversion for “normal” kinetics. The hatched area corresponds to the volume of a CSTR required to give the indicated conversion.
- 3.7.1 Series Reactions
- 3.7.2 Parallel Reactions
- 3.7.3 Series–Parallel Reactions
- Example 3.4
- SOLUTION
- a. CSTR
- b. PFR
- SOLUTION
- Example 3.4
- 3.8.1 Plug Flow Reactors in Series
- FIGURE 3.6 A system of plug flow reactors in series. The entire process stream is fed to the first reactor. The effluent from each reactor forms the feed stream to the next reactor.
- 3.8.2 Plug Flow Reactors in Parallel
- FIGURE 3.7 A system of plug flow reactors in parallel. The total molar flow rate is divided among the reactors in any desired manner.
- 3.8.3 CSTR in Parallel
- FIGURE 3.8 A system of CSTR in parallel. The total process stream is divided up among the reactors. The effluent streams from the reactors are then mixed.
- 3.8.4 CSTR in Series
- FIGURE 3.9 A system of CSTR in series. The entire process stream is fed to the first reactor. The effluent from each reactor forms the feed stream to the next reactor.
- 3.8.4.1 Minimum Total Reactor Volume for CSTR in Series
- FIGURE 3.10 A system of two CSTR in series.
- FIGURE 3.11 Conversion as a function of inverse reaction rate for two CSTR in series. The hatched areas are equal to the reactor volumes.
- Example 3.5
- SOLUTION
- FIGURE 3.12 Representation of CSTR and a PFR in series, with the CSTR placed first.
- FIGURE 3.13 Representation of CSTR and a PFR in series, with the PFR placed first.
- Example 3.6
- SOLUTION
- FIGURE 3.14 Reactor arrangement for Problem 3.6. Two CSTR in series with an additional feed stream to the second reactor.
- SOLUTION
- 3.10.1 Transient Plug Flow Reactor
- 3.10.2 Single Transient CSTR
- 3.10.2.1 Transient CSTR with Constant Volume
- 3.10.2.2 Transient CSTR with Variable Volume: Semibatch Operation
- 3.10.3 Transient CSTR in Series: Constant Volume
- FIGURE 3.15 Two CSTR in series in which a reversible reaction is occurring.
- Case Study 3.2: Transient Operation of CSTR for the Hydrogenation of Oil
- SINGLE REACTOR: CONSTANT VOLUME
- FIGURE 3.16 Dimensionless sulfur and nitrogen concentrations in reactor effluent for the single constant-volume transient CSTR. Results for Case Study 3.2.
- TWO CSTR IN SERIES: CONSTANT VOLUME
- FIGURE 3.17 Dimensionless nitrogen concentrations in reactor effluent for two constant-volume transient CSTR in series. The conversion in the second reactor is higher than the first. Results for Case Study 3.2.
- FIGURE 3.18 Dimensionless sulfur concentrations in reactor effluent for two constant-volume transient CSTR in series. The conversion in the second reactor is higher than the first. Results for Case Study 3.2.
- SINGLE TRANSIENT REACTOR: VARIABLE VOLUME
- FIGURE 3.19 Dimensionless nitrogen and sulfur concentrations in the reactor for a variable volume transient CSTR. (a) The graph shows the behavior during the first 1.271 h when the reactor is being filled. (b) The graph corresponds to constant volume operation. Note that for the sulfur conversion, most of the reaction occurs during the filling stage. Results for Case Study 3.2.
- SINGLE REACTOR: CONSTANT VOLUME
- 4.1 Influence of Temperature on Reactor Operation
- 4.1.1 Temperature Dependence of Reaction Rate Constants
- 4.1.2 Effect of Temperature on Equilibrium Conversion
- 4.1.3 Energy Balance for Ideal Reactors
- 4.2 General Energy Balance
- 4.3 Batch Reactor
- 4.3.1 Constant-Volume Batch Reactor
- 4.3.2 Relationship between ΔUR and ΔHR
- Example 4.1
- SOLUTION
- 4.3.2.1 Assuming a Constant Value for Heat Capacity
- Example 4.1
- 4.3.3 External Heat Transfer in CVBR
- 4.3.4 Adiabatic Temperature Change for CVBR
- Example 4.2
- SOLUTION
- FIGURE 4.1 Time dependence of (a) conversion and (b) temperature for the oxidation of CO in a constant volume batch reactor. Because the reactor is adiabatic and the reaction is exothermic, the temperature rises as the reaction proceeds.
- SOLUTION
- Example 4.2
- FIGURE 4.2 Conversion verses temperature for the oxidation of CO. The line is almost straight, which indicates that the temperature dependence of the heat capacity and internal energy of reaction is not significant.
- Example 4.3
- SOLUTION
- FIGURE 4.3 Time dependence of (a) conversion and (b) temperature for the oxidation of CO in a constant pressure batch reactor. Because the reactor is adiabatic and the reaction is exothermic, the temperature rises as the reaction proceeds.
- SOLUTION
- FIGURE 4.4 Fractional conversion as a function of time for the three pseudocomponents, sulfur, nitrogen, and 343 + material. The sulfur has the highest fractional conversion after 300min.
- FIGURE 4.5 Temperature as a function of time for the batch reactor of Case Study 4.1. Note that the temperature initially increases owing to the exothermic chemical reaction and heat transfer from the surroundings. Later, the temperature starts to decrease as heat is transferred to the surroundings.
- 4.4.1 Basic Energy Balance Equation
- FIGURE 4.6 Incremental reactor volume used to derive the energy balance for a plug flow reactor.
- 4.4.1.1 Use of Average Heat Capacity
- 4.4.2 Temperature and Concentration Profiles as Function of Reactor Length
- 4.4.3 Adiabatic Operation of PFR: Adiabatic Reaction Line
- Example 4.4
- SOLUTION
- Example 4.4
- FIGURE 4.7 Typical configuration for an externally heated or cooled PFR. The central tube serves as the reactor and the jacket contains an appropriate heat transfer fluid. Many other designs are possible.
- FIGURE 4.8 Multitubular reactor used for nonadiabatic operation. The reacting mixture flows through the tubes while the heat transfer fluid flows over the outside. The heat transfer fluid frequently undergoes a phase change.
- Example 4.5
- SOLUTION
- FIGURE 4.9 Axial conversion (a) and temperature (b) profiles for the PFR of Example 4.5. The solid line represents the adiabatic reactor case and the dashed line shows an externally cooled reactor with a constant-temperature heat transfer fluid.
- FIGURE 4.10 Axial conversion (a) and temperature (b) profiles for the PFR of Example 4.5, Part (c). Both the reactor temperature and the coolant temperature exhibit a steady rise. The reactor fluid and the coolant flow in the same direction.
- SOLUTION
- FIGURE 4.11 Axial conversion (a) and temperature (b) profiles for the PFR of Example 4.5, Part (d). Both the reactor temperature and the coolant temperature exhibit a steady increase. Note that the coolant flows in the direction opposite to the fluid in the reactor.
- Case Study 4.2: Hydrogenation of Gas Oil in a Nonisothermal PFR
- FIGURE 4.12 Axial conversion (a) and temperature (b) profiles for the PFR of Case Study 4.2. The reactor temperature initially rises and then falls, typical of cooled PFR with an exothermic reaction.
- Case Study 4.3: Parametric Sensitivity of a Cooled Plug Flow Reactor
- FIGURE 4.13 Axial temperature profile at different values of the heat transfer coefficient. The maximum reactor temperature occurs when the heat transfer coefficient is zero, which corresponds to adiabatic operation.
- FIGURE 4.14 Axial temperature profile at different values of the enthalpy of reaction. The numbers next to each curve are the values of (−ΔHR,343). Note the large spike in the temperature profile that occurs when the enthalpy of reaction is large. In this situation, the temperature in the reactor is limited by conversion of the reactants.
- FIGURE 4.15 Axial conversion profile when (−ΔHR,343) = 600 J/g. The conversion of all three components rapidly increases to a value of one as the temperature rises. This type of reactor operation is usually considered to be undesirable.
- 4.4.7.1 Equilibrium Effects in Endothermic Reactions
- 4.4.7.2 Equilibrium Effects in Exothermic Reactions
- FIGURE 4.16 The equilibrium line shows the relationship between the temperature and fractional conversion at equilibrium for a specified starting composition. The adiabatic reaction line shows the maximum conversion that can be obtained for adiabatic operation for a given inlet temperature. The isothermal reaction line shows the best conversion for isothermal operation.
- FIGURE 4.17 Each solid line in this diagram represents a constant value of reaction rate. The top line is the equilibrium line, where the rate is equal to zero. At higher temperatures, the maximum fractional conversion that can be achieved at any rate drops. The dashed line shows a method of reactor operation that would achieve a minimum total reactor volume.
- 4.4.7.3 Multibed Adiabatic Reactors for Equilibrium Limited Reactions
- FIGURE 4.18 Multiple adiabatic reactors in series can be used to achieve a high level of conversion without cooling the reactor. Each bed is run adiabatically until the equilibrium line is approached. At this point, the process stream is cooled prior to entry to the next bed. The number of beds and the extent of reaction in each bed depend on the reaction and a variety of cost factors.
- FIGURE 4.19 Multiple bed adiabatic catalytic reactor with interstage cooling. This type of design is often used for achieving high conversions in exothermic reactions where the equilibrium tends to limit the reaction yield. A classic industrial application of this design is the oxidation of sulfur dioxide to sulfur trioxide.
- 4.5.1 Steady-State CSTR: Basic Energy Balance
- 4.5.2 Adiabatic Operation of CSTR: Adiabatic Reaction Line
- 4.5.3 External Heat Exchange in CSTR
- Example 4.6
- SOLUTION
- Example 4.6
- FIGURE 4.20 Behavior of the heat removal function at different feed inlet temperatures, with all other operating conditions being the same. An increase in the inlet temperature simply shifts the line to the right.
- FIGURE 4.21 Behavior of the heat removal function at different values of with all other operating conditions the same. The slope of the line changes.
- FIGURE 4.22 Shape of the heat generation function at different reactor temperatures. The curve shape depends on the activation energy.
- FIGURE 4.23 Plot of a single heat generation curve and multiple heat removal curves. Each heat removal curve corresponds to a different reactor inlet temperature.
- FIGURE 4.24 Ignition extinction curve for a CSTR operated at pseudo-steady state. The reactor temperature follows the lower branch of the curve as the feed temperature increases, and then falls along the upper branch as the feed temperature is reduced.
- Example 4.7
- SOLUTION
- FIGURE 4.25 Ignition extinction curve for Example 4.7. The curve shows the possible outlet reactor temperatures for the given inlet temperature. The upper and lower curves represent stable operating points, while the central line represents unstable points.
- SOLUTION
- Example 4.8
- SOLUTION
- FIGURE 4.26 Reactor temperature as a function of time for inlet temperatures of (a) 341.104 K and (b) 341.105 K. At an initial temperature of 341.105K, the reactor temperature crosses the critical threshold, and the final reactor temperature lies on the upper operating line.
- SOLUTION
- Example 4.9
- SOLUTION
- Step 1: First 50min of Operation
- Step 2: Remaining 70min of Operation
- FIGURE 4.27 Time dependence of (a) the moles of the reacting species and (b) the temperature in a semibatch reactor. The feed stream is switched off at 3000s. Results from Example 4.9.
- SOLUTION
- 5.1 General Nature of Rate Functions
- 5.2 Reaction Mechanism
- 5.2.1 Rate Expressions for Elementary Reactions
- 5.2.2 Rate Expressions for Nonelementary Reactions
- 5.3 Theoretical Analysis of Reaction Rate
- 5.3.1 Collision Theory
- 5.3.2 Absolute Reaction Rate Theory
- FIGURE 5.1 Potential energy plot of a chemical reaction. The reactants must pass over the energy barrier to become products. The activated complex sits at the top of the energy barrier.
- 5.3.3 Temperature Dependence of Rate Constant
- FIGURE 5.2 Typical temperature dependence of the reaction rate constant observed in practice. This plot is often called an Arrhenius plot.
- 5.4.1 Unimolecular Reactions
- 5.4.1.1 Lindeman Mechanism
- 5.4.1.2 Steady-State Hypothesis for Lindeman Mechanism
- 5.4.2 Rice–Herzfeld Mechanisms
- 5.4.3 Complex Gas-Phase Reactions
- 5.4.4 Rate-Determining Step Method for Deriving Rate Expressions
- 5.6.1 Rate Data in Constant-Volume Batch Reactor
- 5.6.2 Differential Method of Analysis of CVBR Data
- FIGURE 5.3 Typical concentration versus time curve that may be obtained in a constant-volume batch reactor. In this case, A is a reactant.
- 5.6.2.1 Finite Difference Formulae
- 5.6.2.2 Fitting a Curve to the Data
- 5.6.3 Determining Form of Rate Expression
- 5.6.3.1 Power Law Models
- FIGURE 5.4 A plot of the ln of the rate as a function of the ln of the concentration of reactant A. The random nature of the deviation of the experimental points from the line indicate that the model may be appropriate.
- FIGURE 5.5 The plot ln of the rate vs. ln of the concentration shows a systematic deviation about the best fit line, indicating that a power law equation may not be the best model for this reaction.
- Example 5.1
- SOLUTION
- FIGURE 5.6 Reaction rate plotted as a function of reactant concentration on a log–log scale. The line is the least squares fit of the data points. It appears that these data follow a power law kinetic model.
- SOLUTION
- 5.6.3.1 Power Law Models
- Example 5.2
- SOLUTION
- FIGURE 5.7 These plots are the linearized version of the reaction rate expression for Example 5.2. Graph (a) corresponds to Equation 5.126, graph (b) corresponds to Equation 5.127, and graph (c) corresponds to Equation 5.128. The straight lines are the regression lines obtained by linear least squares analysis.
- FIGURE 5.8 Comparison of the predicted reaction rate at various concentration of A from the four different sets of reaction rate parameters. The four lines are virtually indistinguishable, indicating that all four parameter sets give the same level of accuracy.
- SOLUTION
- 5.6.4.1 Power Law Kinetics
- FIGURE 5.9 Integral method plot for a uni-molecular reaction with a power law rate equation. The value of n must give a straight line of slope equal to the value of the rate constant.
- 5.6.4.2 Complex Kinetics
- Example 5.3
- SOLUTION
- FIGURE 5.10 Half-life plotted as a function of reactant concentration on a log–log scale. The line is the least squares fit of the data points. The slope of the line is equal to −0.5462.
- SOLUTION
- Example 5.3
- 5.6.6.1 Method of Isolation
- 5.6.6.2 Method of Excess
- Example 5.4
- SOLUTION
- Example 5.4
- 6.1 Causes of Nonideal Reactor Behavior
- 6.1.1 Nonideal Behavior in CSTR
- 6.1.2 Deviations from Plug Flow Performance
- FIGURE 6.1 Typical CSTR illustrating possible causes of nonideal performance. Badly placed inlet and outlet lines can cause feed bypassing, and poorly designed impellers and baffles can result in the formation of dead zones.
- 6.1.3 Deviations from Perfect Mixing in Batch and Fed Batch Reactors
- 6.2 Residence Time and Mixing
- 6.3 RTD Function
- 6.3.1 Measurement of RTD
- 6.3.2 RTD Function
- FIGURE 6.2 Typical residence time distribution function for a flow system. The density function can be used to determine deviations from ideal reactor performance.
- 6.3.3 Cumulative Distribution and Washout Functions
- 6.3.4 Determination of f(t) from Pulse Input
- FIGURE 6.3 Typical cumulative distribution function for a flow system. The cumulative distribution function gives the fraction of particles with a residence time less than t. The cumulative distribution function can be obtained by integrating the density function.
- FIGURE 6.4 Typical washout function for a flow system. The washout function gives the fraction of particles with a residence time greater than t. It can be obtained from the residence time density function.
- 6.3.5 Determination of f(t) from Step Change
- 6.3.6 Means and Moments
- 6.3.7 Normalized RTD Functions
- Example 6.1
- SOLUTION
- FIGURE 6.5 Concentration versus time plot of the experimental data for Example 6.1. The experimental points have simply been connected by straight lines.
- FIGURE 6.6 Residence time distribution function obtained by integrating the experimental concentration–time data for Example 6.1. As with Figure 6.5, the data points have been connected by straight lines.
- FIGURE 6.7 The cumulative distribution function for the data of Example 6.1. The curve progresses from a value of zero to one as all of the tracer molecules leave the system.
- FIGURE 6.8 Washout function for the data of Example 6.1. This line is the mirror image of the cumulative distribution function shown in Figure 6.7.
- SOLUTION
- Example 6.1
- 6.4.1 RTD in Perfectly Mixed CSTR
- 6.4.2 RTD in Plug Flow System
- FIGURE 6.9 Response of a plug flow system to a step increase in inlet tracer concentration. The lack of axial mixing implies that the outlet response curve has the same shape as the inlet change.
- 6.5.1 Multiple Vessel Models
- 6.5.1.1 Parallel Plug Flow Reactors
- 6.5.1.2 Fractional Tubularity Model
- FIGURE 6.10 Any RTD can be approximated using a system of parallel PFR. The length of the reactors is adjusted to match the washout function.
- FIGURE 6.11 The fractional tubularity model is one of the simplest multiple vessel models. It models the reactor as a PFR and a CSTR in series. The RTD is the same regardless of the order of the reactors.
- FIGURE 6.12 The washout function for the fractional tubularity model is characterized by a sharp first appearance followed by an exponential tail. The point of breakthrough depends on the relative volume of the PFR.
- 6.5.1.3 Tanks-in-Series Model
- FIGURE 6.13 The tanks-in-series model uses a number of equally sized CSTR placed in series. The volume of each reactor is the total volume divided by the number of reactors.
- FIGURE 6.14 The shape of the washout function from the tanks-in-series model depends on the number of tanks. For one tank, the washout function is exponential, while as the number of tanks increases, the performance approaches that of a plug flow system.
- Example 6.2
- SOLUTION
- FIGURE 6.15 The shape of the residence time distribution function with an increasing number of tanks. The curve tends to become more symmetrical and, in the limit, becomes a Gaussian distribution.
- FIGURE 6.16 A portion of the residence time distribution curve for the tanks-in-series model with 100 tanks.
- 6.5.1.4 Extensions of Tanks in Series: Gamma Function and Fractional Tanks
- FIGURE 6.17 RTD curves for the gamma function model. The gamma function model can account for stagnant regions and bypassing in CSTR.
- Example 6.3
- SOLUTION
- FIGURE 6.18 Comparison of the dimensionless variance for the gamma function model (solid line) and the fractional tanks model (dashed line).
- SOLUTION
- FIGURE 6.19 The backflow cell model is essentially a tanks-in-series, model which allows fluid to flow backwards to upstream tanks.
- FIGURE 6.20 The crossflow model has a separate stirred tank attached to the main tank. Fluid is transferred between the two at a specified flow rate. This model can be used for a CSTR with stagnant regions.
- FIGURE 6.21 Side capacity models come in various forms and are another model that can be used to account for stagnant regions.
- FIGURE 6.22 Comparison of the outlet response to a step input for plug flow and flow with axial dispersion.
- FIGURE 6.23 The washout function depends on the value of the Peclet number. At small Peclet number, the performance is similar to a CSTR, and as the Peclet number increases the behavior approaches plug flow.
- FIGURE 6.24 A near Gaussian-shaped distribution function for the dispersion model with high Peclet number. In this case, the Peclet number is 100.
- Example 6.4
- SOLUTION
- 6.5.4.1 Taylor–Aris Dispersion
- FIGURE 6.25 The fractional tubularity model gives the same RTD function regardless of the order of the reactions. For any reaction other than first order, the conversion from the two reactor systems will be different.
- 6.6.1 Laminar and Turbulent Mixing
- 6.6.2 Mixing Process: Micromixing and Macromixing
- 6.6.2.1 Macromixing and Macrofluids
- 6.6.2.2 Micromixing and Microfluids
- 6.6.2.3 Mixing and RTD
- 6.6.3 Segregated Tank Reactor
- FIGURE 6.26 Different levels of mixing in a stirred tank. (a) The “packages” of fluid are perfectly mixed in the vessel, but each package maintains its integrity as it flows through the vessel. (b) Each package is broken up and mixed with the vessel contents. The RTD for each vessel is the same.
- 6.6.3.1 Conversion in Segregated Tank Reactor
- Example 6.5
- SOLUTION
- Example 6.5
- FIGURE 6.27 The segregated flow model for mixing can be envisaged as a plug flow reactor with multiple outlet streams. All the fluid enters at the reactor inlet, and then outlet side streams are added to match the observed residence time distribution.
- FIGURE 6.28 The maximum mixedness flow model for mixing can be envisaged as a plug flow reactor with multiple inlet streams. The fluid enters at specified inlet side streams, whose positions are added to match the observed residence time distribution.
- FIGURE 6.29 Control volume used to develop the mole balance for the maximum mixedness model.
- FIGURE 6.30 The bounding of the micro- and macromixing regions are shown. For flow without bypassing, the conversion is bounded by a region delineated by the PFR, the perfectly mixed CSTR, and the segregated tank reactor.
- FIGURE 6.P1 Arrangement of tanks and flows for Problem 6.1.
- FIGURE 6.P2 Arrangement of tanks and flows for Problem 6.2.
- FIGURE 6.P10 Outlet RTD curves for the vessels in Problem 6.10.
- 7.1 Origins of Catalysis: Historical Perspectives
- 7.2 Definitions and Fundamental Concepts
- 7.2.1 Classification by Number of Phases
- 7.2.2 Catalyst Activity and Active Sites
- 7.2.3 Adsorption
- 7.2.4 Selectivity and Functionality
- 7.3 Thermodynamics
- FIGURE 7.1 Energy plot for a heterogeneous catalytic reaction. The catalyst lowers the energy barrier for reaction, compared to the noncatalytic reaction, and thus increases the reaction rate.
- 7.4 Catalyst Types and Basic Structure
- 7.4.1 Basic Catalyst Structure
- FIGURE 7.2 Examples of typical porous structures. (a) A structure of random capillaries; (b) spheres of different sizes fused together; and (c) a structure of irregular pores with dead-end volume.
- FIGURE 7.3 A typical bimodal pore size distribution.
- 7.4.2 Supported Catalysts
- 7.4.3 Metal Catalysts
- 7.4.4 Deactivation
- 7.4.1 Basic Catalyst Structure
- 7.5 Classification of Vapor-Phase Reactions
- 7.5.1 Acid-Catalyzed Reactions
- 7.5.1.1 Catalytic Cracking
- 7.5.1.2 Alkylation
- 7.5.1.3 Isomerization
- 7.5.1.4 Polymerization
- 7.5.1.5 Hydrogen Transfer
- 7.5.2 Hydrogenation–Dehydrogenation
- 7.5.2.1 Carbon Bond Saturation or Reverse
- 7.5.2.2 Hydrogenation of Aromatics and Aromatization
- 7.5.2.3 Dehydrogenation of Oxyorganic Compounds without Water Removal
- 7.5.2.4 Hydrogenolysis of Carbon–Oxygen or Nitrogen–Oxygen Bonds
- 7.5.2.5 Hydrogenolysis of Oxides of Carbon
- 7.5.2.6 Hydrodesulfurization
- 7.5.2.7 Ammonia Synthesis
- 7.5.3 Oxidation
- 7.5.3.1 Oxygen Addition Reactions
- 7.5.3.2 Oxygenolysis
- 7.5.4 Hydration and Dehydration
- 7.5.5 Dehydration–Dehydrogenation
- 7.5.6 Isotope Exchange
- 7.5.7 Miscellaneous
- 7.5.1 Acid-Catalyzed Reactions
- 7.6 Basic Steps in Heterogeneous Catalytic Reactions
- FIGURE 7.4 Simplified diagram of the processes occurring in a solid-catalyzed reaction. Transport effects are often as important as the kinetic effects. The lines in the solid represent pores.
- 7.7 Introduction to Catalytic Reactors
- 7.7.1 Fixed Bed Reactor
- 7.7.2 Fluidized Bed Reactor
- FIGURE 7.5 Illustration of a fixed bed catalytic reactor. A porous bed of catalyst particles is fixed in a tube, and the reactants pass the bed. The fixed bed reactor is simple to build and operate.
- FIGURE 7.6 Illustration of a fluidized bed reactor. The high-velocity gas causes the catalyst bed to behave like a fluid, which gives good heat and mass transfer.
- 7.7.3 Reactors for Liquids and Gas/Liquid Mixtures
- 7.7.3.1 Trickle Bed Reactor
- 7.7.3.2 Slurry Reactor
- FIGURE 7.7 Illustration of a trickle bed reactor. Typically, the bed is mounted vertically, and both liquid and gaseous reactants flow cocurrently through the bed. This reactor type exhibits complex behavior.
- FIGURE 7.8 Illustration of a slurry reactor. The fine catalyst particles are suspended in the liquid by the action of the impeller. In this example, a gas is bubbled through the liquid using a sparger.
- 8.1 Adsorption
- 8.1.1 Physical Adsorption
- 8.1.2 Chemisorption
- FIGURE 8.1 Chemical adsorption (chemisorption) of species on a surface. In (a), the methane molecule dissociates as it adsorbs. In (b), three possible mechanisms are shown for the adsorption of CO. It can adsorb on a single active site, two sites or it can dissociate as it adsorbs.
- 8.1.3 Differentiating Chemical and Physical Adsorption
- 8.1.4 Energetics of Adsorption
- FIGURE 8.2 Simplified potential energy diagram for physical adsorption. The zero potential energy line represents an infinite separation distance. As the adsorbate approaches the surface, a balance is established between the forces of attraction and repulsion.
- 8.1.4.1 Activated Chemisorption
- FIGURE 8.3 Simplified potential energy diagram for dissociative activated chemisorption. As molecules approach the surface, they first become physically adsorbed. If the physically adsorbed molecule can attain sufficient activation energy, it can become chemisorbed in the dissociated state.
- 8.1.4.2 Nonactivated Chemisorption
- FIGURE 8.4 Simplified potential energy diagram for dissociative nonactivated chemisorption. As molecules approach the surface, they first become physically adsorbed, but no activation energy is required for the physically adsorbed molecules to move to the chemisorbed state.
- 8.1.4.3 Endothermic Adsorption
- 8.1.4.4 Dual Site Adsorption
- FIGURE 8.5 Potential energy diagram for endothermic dissociative chemisorption. This type of adsorption is rare but has been shown to occur.
- FIGURE 8.6 Potential energy diagram for dual site adsorption. The chemisorption on type x sites is nonactivated. Chemisorption on type y sites may or may not be activated, depending on the path followed.
- 8.1.5 Equilibrium Adsorption
- FIGURE 8.7 Potential energy diagram for dual site adsorption. The chemisorption on both type x and y sites is activated.
- 8.1.5.1 Adsorption Isotherms
- 8.1.5.2 Models for Adsorption Isotherms
- FIGURE 8.8 Typical adsorption isotherms. The amount adsorbed increases with pressure, and typically falls as the temperature increases.
- 8.1.5.3 Adsorption Isobars
- FIGURE 8.9 Typical adsorption isobars. Higher pressures result in an increase in the amount adsorbed at equilibrium. The amount adsorbed often decreases as the temperature increases.
- 8.1.5.4 Adsorption Isoteres
- 8.1.6 Heat of Adsorption
- FIGURE 8.10 Typical adsorption isoteres. Each curve represents a line of constant coverage, which changes with temperature and pressure.
- FIGURE 8.11 Behavior of the heat of adsorption as a function of surface coverage. The value may remain constant or decline as coverage increases.
- FIGURE 8.12 The heat of adsorption at any given surface coverage can be calculated from two adsorption isotherms.
- 8.1.7 Langmuir Adsorption Model: Detailed Consideration
- 8.1.7.1 The Langmuir Model: Single-Component Systems
- FIGURE 8.13 Pathway for the molecular adsorption of molecule A on a surface site.
- 8.1.7.2 Langmuir Model: Dissociative Chemisorption
- FIGURE 8.14 Pathway for the dissociative adsorption of diatomic molecule A2 on two surface sites.
- 8.1.7.3 Langmuir Model: Multicomponent Systems, Single Site Type
- FIGURE 8.15 Pathway for the competitive molecular adsorption of molecules A and B on the surface sites.
- 8.1.7.1 The Langmuir Model: Single-Component Systems
- 8.2.1 Langmuir–Hinshelwood–Hougen–Watson Rate Equations
- FIGURE 8.16 Sequence of elementary steps for LHHW model, Case 1. A and B adsorb as molecules, react to form adsorbed molecules of C and D, which subsequently desorb.
- FIGURE 8.17 Steps in the reaction mechanism for LHHW Case 3. The mechanism involves the dissociative chemisorption of two reactants.
- FIGURE 8.18 Eley–Rideal mechanism. Molecules of A adsorb on the catalyst surface, which then react with B molecules in the gas phase. LHHW Case 5.
- FIGURE 8.19 Steps in a dual site model. The catalyst surface has two different types of sites, which selectively adsorb certain species. LHHW Case 6.
- 8.2.1.1 General Form of LHHW Reaction Models
- FIGURE 8.20 Reaction rate as a function of concentration of A for a typical LHHW-type rate expression. The volcano shape results from a competition between the kinetic-driving force and the adsorption inhibition term.
- Example 8.1
- SOLUTION
- 9.1 Diffusion in Bulk Phase
- 9.1.1 Basics of Bulk Diffusion: Diffusion Coefficient
- 9.1.2 Calculating Molecular Diffusion Coefficients in Binary Systems
- 9.1.3 Total Molar Diffusive Flux in Binary System
- 9.1.4 Diffusion in Multicomponent Mixtures: Generalized Fick's Law
- 9.1.5 Multicomponent Diffusion in Dilute Mixtures
- 9.2 External Mass and Heat Transfer Effects
- 9.2.1 Mass and Heat Transfer Coefficients
- FIGURE 9.1 The development of velocity, temperature, and concentration boundary layers for flow across a flat plate. Regardless of the shape, a boundary layer will be present at the fluid–solid boundary.
- 9.2.2 Effect of External Mass Transfer on Observed Reaction Rate
- FIGURE 9.2 The apparent activation for a reaction changes as the external mass transfer effects become significant.
- 9.2.3 Combined Heat and Mass Transfer
- 9.2.4 Effect of External Transport on Selectivity
- 9.2.4.1 Isothermal Series Reaction
- 9.2.4.2 Parallel Isothermal Reactions
- 9.2.4.3 Nonisothermal Reactions
- 9.2.1 Mass and Heat Transfer Coefficients
- 9.3.1 Diffusion in Catalyst Pores
- 9.3.2 Effective Diffusivity
- 9.3.3 Parallel Pore Model
- Example 9.1
- SOLUTION
- Example 9.1
- Example 9.2
- SOLUTION
- Example 9.3
- SOLUTION
- 9.4.1 Effectiveness Factor
- FIGURE 9.3 Effect of temperature and pressure on the diffusion coefficients of methane. Top graph shows the pressure of 1bar. The short dashed line represents the pore diffusion coefficient. The bottom graph shows the results from a pressure of 20 bars. Note the difference in scales for the diffusion coefficient axis in the two graphs.
- 9.4.2 Effectiveness Factor for Isothermal Flat Plate
- FIGURE 9.4 Representation of a flat slab of catalyst. In (a), the diffusion occurs from each side of the slab, while in (b), the diffusion occurs from one side only with the other side sealed. The situations are mathematically the same.
- 9.4.2.1 Thiele Modulus for First-Order Reaction
- 9.4.2.2 Effectiveness Factor for First-Order Reaction in Flat Plate
- FIGURE 9.5 Effectiveness factor plots for the three one-dimensional geometries.
- 9.4.2.3 Asymptotic Solutions for Effectiveness Factor
- Example 9.4
- SOLUTION
- Example 9.4
- FIGURE 9.6 Effectiveness factor plots for the three one-dimensional geometries using the generalized Thiele modulus.
- FIGURE 9.7 Effectiveness factor plots for a reaction with LHHW-type kinetics. The value of Γ varies (see Equation 9.151).
- 9.4.7.1 Solving Coupled Mole and Energy Balance Equations
- FIGURE 9.8 Effectiveness factor plots for a nonisothermal catalyst pellet with different values of β and γ = 20.
- 9.4.7.2 Solution Algorithm Using Only Initial Value Problems
- FIGURE 9.9 Effect of internal mass transfer limitation on the apparent activation energy of reaction. For a first-order reaction, the apparent activation energy falls by one-half as the reaction becomes completely mass transfer controlled.
- Example 9.5
- SOLUTION
- FIGURE 9.P2 Tube wall reactor used in Problem 9.2.
- 10.1 Packed-Bed Reactor: Introduction and Overview
- 10.2 Conservation Equations for Packed Beds
- 10.2.1 Momentum Balance in Packed Beds
- 10.2.1.1 Velocities in Packed Beds
- 10.2.1.2 One-Dimensional Flow
- Example 10.1
- SOLUTION
- Example 10.1
- 10.2.1.3 Ergun Equation
- 10.2.1.4 Deriving the Ergun Equation
- 10.2.1.5 Continuity Equation
- Example 10.2
- SOLUTION
- Example 10.2
- 10.2.1 Momentum Balance in Packed Beds
- 10.3.1 Pseudo-Homogeneous Model for an Adiabatic-Packed Bed
- FIGURE 10.1 Elemental reactor volume element used for developing the mole and energy balance equations for an adiabatic-packed bed.
- 10.3.1.1 Steady-State Mole Balance Equation
- 10.3.1.2 Steady-State Energy Balance Equation
- 10.3.2 Heterogeneous Model for an Adiabatic-Packed Bed
- 10.3.2.1 Steady-State Mole Balance Equation for the Fluid
- 10.3.2.2 Steady-State Mole Balance Equation for the Solid Catalyst
- 10.3.2.3 Steady-State Energy Balance Equation for the Fluid
- 10.3.2.4 Steady-State Energy Balance Equation for the Solid Catalyst
- Example 10.3
- SOLUTION
- Example 10.3
- FIGURE 10.2 Elemental reactor volume element used for developing the mole and energy balance equations for a nonadiabatic-packed bed.
- 10.3.4.1 Heat Transfer Coefficient for Nonadiabatic Reactors
- 10.4.1 Pseudo-Homogeneous Axial Dispersion Model
- 10.4.1.1 Mole Balance Equation
- 10.4.1.2 Energy Balance Equation
- 10.4.1.3 Boundary Conditions for the 1D Axial Dispersion Model
- 10.4.2 Heterogeneous Axial Dispersion Model
- 10.4.2.1 Mole Balance Equations
- 10.4.2.2 Energy Balance Equation in the Fluid Phase
- 10.4.2.3 Energy Balance Equation for the Solid Phase
- 10.4.2.4 Boundary Conditions
- 10.5.1 Pseudo-Homogeneous 2D Model
- 10.5.1.1 Fluid Transport Mechanisms Are Dispersion Only Mole Balance Equation
- FIGURE 10.3 Elemental reactor volume element used for developing the mole and energy balance equations for the two-dimensional packed-bed reactor model. (a) Shows a typical cylindrical reactor and coordinate system, while (b) shows the elemental volume element.
- 10.5.1.2 Energy Balance Equation
- 10.5.1.3 Boundary Conditions
- 10.5.1.1 Fluid Transport Mechanisms Are Dispersion Only Mole Balance Equation
- 10.5.2 Heterogeneous 2D Model
- 10.5.2.1 Mole Balance Equation for the Fluid
- 10.5.2.2 Mole Balance Equation for the Solid
- 10.5.2.3 Energy Balance Equation for the Fluid
- 10.5.2.4 Energy Balance Equation for the Solid
- 10.5.2.5 Boundary Conditions
- 10.6.1 One-Dimensional Reactor: Pseudo-Homogeneous Case
- 10.6.2 One-Dimensional Reactor: Heterogeneous Case
- 10.6.3 Two-Dimensional Reactor: Pseudo-Homogeneous Case
- 10.6.4 Two-Dimensional Reactor: Heterogeneous Case
- 10.7.1 Fluid/Solid Mass and Heat Transfer Coefficients
- Example 10.4
- SOLUTION
- Example 10.4
- Example 10.5
- SOLUTION
- Example 10.6
- SOLUTION
- FIGURE 10.4 Adiabatic-packed-bed reactor with feed preheat using the reactor effluent. The amount of preheat can be controlled by bypassing the heat exchanger with a portion of the feed. This design can have multiple steady-state operating points.
- FIGURE 10.5 Reactor with feed preheat in a nonadiabatic arrangement. This reactor can also exhibit multiple steady states for some operating conditions.
- FIGURE 10.6 Pressure drop across the bed as a function of fluid velocity, with the associated flow regimes. (a) Fixed bed, (b) bubbly flow, (c) slug flow, and (d) complete particle entrainment.
- FIGURE 10.7 Schematic of a fluidized-bed catalytic cracker. This design is one of many that exist.
- 10.9.1 Minimum Fluidization Velocity
- 10.9.1.1 Entrainment Velocity
- 10.9.1.2 Fluid-Bed Reactor Modeling
- FIGURE 10.8 Schematic of a counter diffusive radiant heater.
- FIGURE 10.9 Photograph of the pads used in a counter diffusive radiant heater. On the left is a pad impregnated with catalyst, and on the right is an insulation pad.
- 10.12.1 Structure and Properties of Monoliths
- FIGURE 10.10 End view of a monolith honeycomb type reactor. The square ceramic substrate has 400 CPSI.
- FIGURE 10.11 Close up view of the 400 CPSI ceramic monolith showing the catalytic washcoat. Note that the washcoat is not uniformly distributed.
- FIGURE 10.12 End view of a metal monolith honeycomb type reactor. The spiral wound monolith is made from thin sheets of corrugated metal.
- FIGURE 10.13 Close up view of the metal monolith showing the catalytic washcoat. Note that the washcoat is also not uniformly distributed and there is a large accumulation in the corners.
- 10.12.2 Analysis of Gas Phase Monolith Reactors
- 10.12.2.1 Complete Converter Models
- FIGURE 10.14 Cross-sectional representation of a monolith channel showing the heat and mass transfer phenomena that occur. Drawing is not to scale.
- 10.12.2.2 Single Channel Models
- FIGURE 10.15 Geometric transformation used to represent the real geometry as a right circular cylinder with annular layers of washcoat and substrate. The area inside the dashed square is mapped. Drawing not to scale.
- 10.12.2.3 A 1D Single Channel Monolith Model
- 10.12.2.1 Complete Converter Models
- 10.13.1 Slurry Reactors
- 10.13.2 Trickle-Bed Reactors
- 11.1 Kinetic Investigations
- 11.1.1 Laboratory Reactor Types
- 11.1.2 Experimental Tubular Reactor
- 11.1.2.1 Isothermal Conditions Maintained in Reactor
- 11.1.2.2 Adiabatic Operation
- 11.1.2.3 Differential Operation
- 11.1.2.4 Integral Operation
- FIGURE 11.1 Conversion curves obtained in a tubular reactor under different conditions.
- 11.1.2.5 Testing for Mass Transfer Limitations
- FIGURE 11.2 Testing for internal diffusion resistance with increasing particle diameter. If the fractional conversion is independent of the particle size then internal resistance is negligible.
- FIGURE 11.3 Testing for external diffusion resistance at constant W/F ratio with increasing flow rate. If the fractional conversion is independent of the flow rate, then external resistance is negligible.
- FIGURE 11.4 Testing for external diffusion resistance at variable W/F ratio with different catalyst mass. If the fractional conversion is the same for both masses of the catalyst, then external resistance is negligible. In (a), the conversion is not the same, so external diffusion resistance is important. In (b), both curves are coincident, so the external diffusion resistance is negligible.
- 11.1.3 CSTR-Like Reactors
- 11.1.3.1 Berty Reactors
- FIGURE 11.5 Some different configurations possible for Berty-type reactors. (a) Catalyst coated on the wall with centrally mounted impellers, (b) catalyst pellets in an annulus with central impeller, (c) catalyst in an annular basket with bottom mounted impeller, and (d) centrally mounted catalyst basket with bottom impeller.
- 11.1.3.2 Carberry (Spinning Basket) Reactor
- FIGURE 11.6 The Notre Dame spinning basket reactor.
- 11.1.3.3 Transport Limitations in Catalytic CSTR
- 11.1.3.4 External Recycle Reactor
- FIGURE 11.7 Testing for external diffusion resistance with increasing speed. If the fractional conversion is independent of speed, then external resistance is negligible.
- FIGURE 11.8 A recycle reactor. The reactor itself operates in plug flow, and a significant portion of the reactor effluent is recycled to the reactor inlet. At very high recycle rates, the reactor operates as a CSTR.
- 11.1.3.1 Berty Reactors
- 11.2.1 Calculation of Surface Area
- FIGURE 11.9 Examples of the five types of adsorption isotherms reported by Brunauer et al. (1940).
- 11.2.2 Pore Volume and Pore Size Distribution
- 11.2.2.1 Pore Size Distribution from Capillary Condensation Data
- 11.2.2.2 Pore Size Distribution from Mercury Porosimetry
- 11.2.2.3 Representations of Pore Size Distribution
- FIGURE 11.10 Cumulative pore volume for a monolith substrate.
- FIGURE 11.11 Pore size distribution for monolith substrate.
- FIGURE 11.12 Cumulative pore volume for monolith with catalytic washcoat.
- FIGURE 11.13 Pore size distribution for catalytic washcoat.
- FIGURE 11.14 Schematic of a Wicke–Kallenback cell used for measuring effective diffusion coefficients.
- 11.3.1 Transmission Electron Microscopy
- 11.3.2 Scanning Electron Microscopy
- Appendix 1: Numerical Methods
- A1.1 Nonlinear Algebraic Equations
- FIGURE A1.1 Newton–Raphson approximation.
- A1.1.1 Convergence
- A1.2 Linear Algebraic Equations
- A1.2.1 Gauss Elimination Method
- A1.2.2 Jacobi and Gauss Seidel Iterative Methods
- A1.3 Ordinary Differential Equations
- A1.3.1 Single Differential Equation
- A1.3.2 Euler's Method
- A1.3.3 Runge–Kutta Methods
- A1.3.3.1 First-Order and Second Runge–Kutta Methods
- A1.3.3.2 Classical Fourth-Order Runge–Kutta Method
- A1.3.3.3 Order and Stability Function
- A1.3.3.4 Implicit RK Methods
- A1.3.4 Linear Multistep Methods
- A1.3.4.1 Backward Differentiation Formula Methods
- A1.3.4.2 Predictor–Corrector Methods: Milne Method
- A1.1 Nonlinear Algebraic Equations
- A1.4 Numerical Integration
- A1.4.1 Trapezoidal Rule
- FIGURE A1.2 Illustration of the trapezoidal rule.
- A1.4.2 Simpson's One-Third Rule
- A1.4.3 Simpson's Three-Eighth Rule
- A1.4.4 Assessment of Accuracy of above Methods
- A1.4.1 Trapezoidal Rule
- A1.5 Numerical Differentiation
- A1.6 Partial Differential Equations
- TABLE A2.1 Enthalpy of Formation, Free Energy of Formation and Heat Capacity Data for Selected Compounds
- TABLE A2.2 Critical Properties of Selected Compounds
- Reference
- A4.1 POLYMATH (http://www.polymath-software.com)
- A4.2 MATLAB® (http://www.mathworks.com)
- A4.3 COMSOL Multiphysics (http://www.comsol.com)
UM RAFBÆKUR Á HEIMKAUP.IS
Bókahillan þín er þitt svæði og þar eru bækurnar þínar geymdar. Þú kemst í bókahilluna þína hvar og hvenær sem er í tölvu eða snjalltæki. Einfalt og þægilegt!Rafbók til eignar
Rafbók til eignar þarf að hlaða niður á þau tæki sem þú vilt nota innan eins árs frá því bókin er keypt.
Þú kemst í bækurnar hvar sem er
Þú getur nálgast allar raf(skóla)bækurnar þínar á einu augabragði, hvar og hvenær sem er í bókahillunni þinni. Engin taska, enginn kyndill og ekkert vesen (hvað þá yfirvigt).
Auðvelt að fletta og leita
Þú getur flakkað milli síðna og kafla eins og þér hentar best og farið beint í ákveðna kafla úr efnisyfirlitinu. Í leitinni finnur þú orð, kafla eða síður í einum smelli.
Glósur og yfirstrikanir
Þú getur auðkennt textabrot með mismunandi litum og skrifað glósur að vild í rafbókina. Þú getur jafnvel séð glósur og yfirstrikanir hjá bekkjarsystkinum og kennara ef þeir leyfa það. Allt á einum stað.
Hvað viltu sjá? / Þú ræður hvernig síðan lítur út
Þú lagar síðuna að þínum þörfum. Stækkaðu eða minnkaðu myndir og texta með multi-level zoom til að sjá síðuna eins og þér hentar best í þínu námi.
Fleiri góðir kostir
- Þú getur prentað síður úr bókinni (innan þeirra marka sem útgefandinn setur)
- Möguleiki á tengingu við annað stafrænt og gagnvirkt efni, svo sem myndbönd eða spurningar úr efninu
- Auðvelt að afrita og líma efni/texta fyrir t.d. heimaverkefni eða ritgerðir
- Styður tækni sem hjálpar nemendum með sjón- eða heyrnarskerðingu
- Gerð : 208
- Höfundur : 8527
- Útgáfuár : 2012
- Leyfi : 380